Defect root cause translator: Translate defect descriptions into root cause findings
The defect root cause translator helps operations teams document defects, analyze causes, and improve performance with ease.
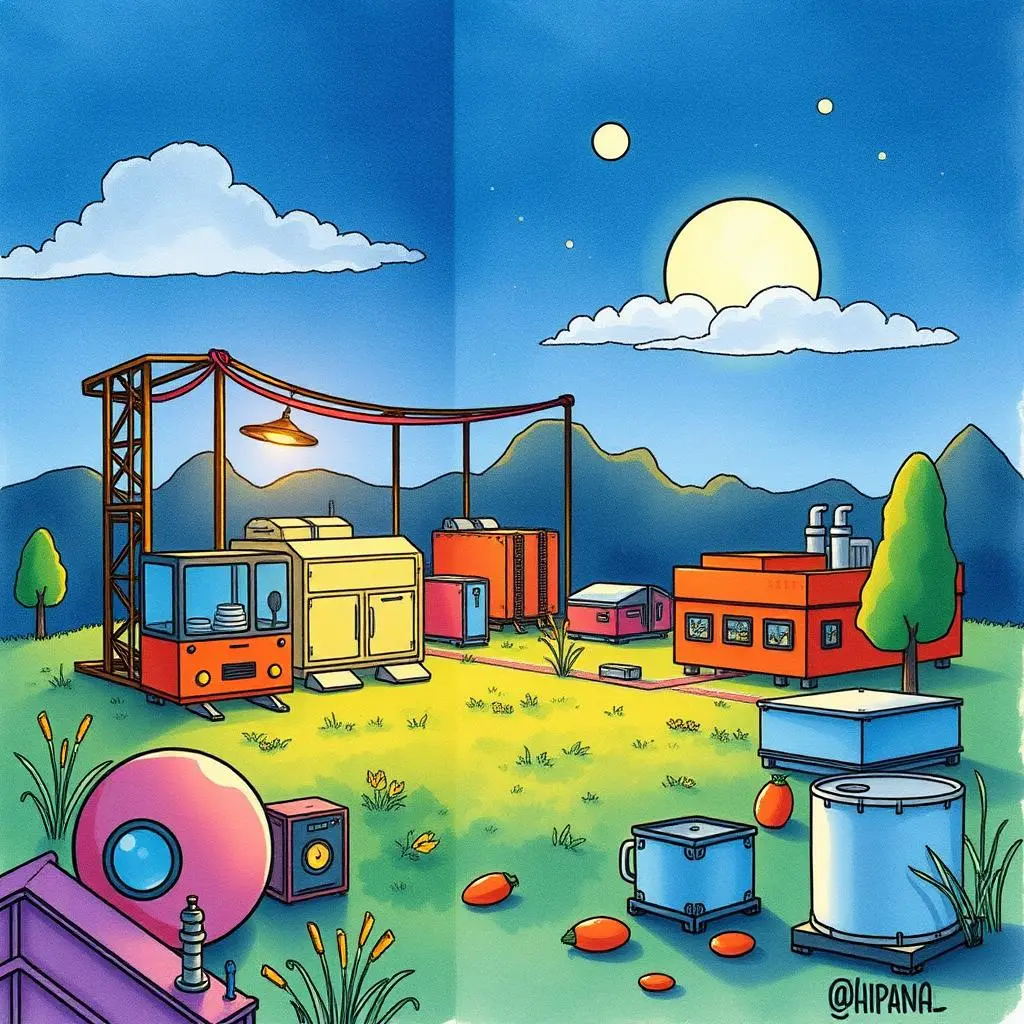
Similar apps
Unlock root cause insights with our defect translator tool
Effortlessly transform defect descriptions into actionable insights
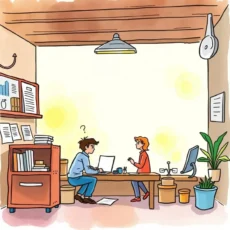
Input detailed defect descriptions for accurate outcomes
Easily input comprehensive defect descriptions to ensure accurate root cause findings. This feature allows the user to detail any defects in their production process, enabling precise translations into actionable insights that drive performance improvement and operational excellence.
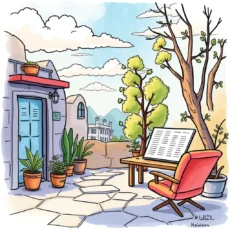
Specify production line for enhanced context
By selecting the specific production line affected by a defect, users provide crucial context. This feature helps narrow down potential root causes based on operational nuances, leading to more targeted corrective actions and streamlined productivity across different production environments.
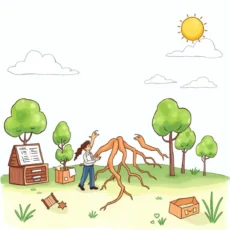
Record critical time stamps for better tracking
Capturing the date and time of occurrence is vital for effective performance monitoring. This feature allows users to log precise incident timing, facilitating trend analysis and identification of recurring issues in the manufacturing process that need immediate attention.
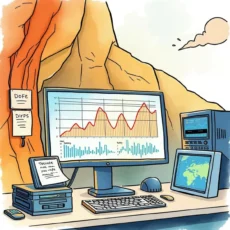
Identify operators involved for root cause analysis
Users can enter the name of the operator involved in a defect incident. Understanding who was operating machinery at the time increases accountability and can reveal patterns or training needs while supporting effective resolution strategies.
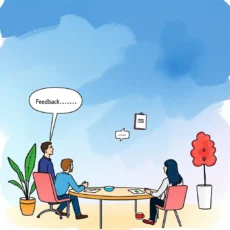
Machine identification enhances diagnostic capabilities
Entering machine IDs or names enables detailed diagnostics related to defect origins. With this information, users can correlate machine performance data with defects, providing a clearer picture of equipment reliability and pinpointing areas for maintenance or upgrades.
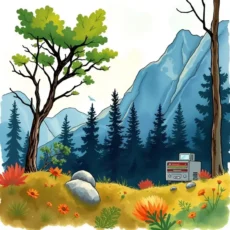
Shift details support comprehensive analysis
Logging whether incidents occur during day or night shifts aids in uncovering shift-related trends impacting quality. This feature empowers analysts to assess workforce effectiveness and align operational strategies accordingly for continuous improvement.
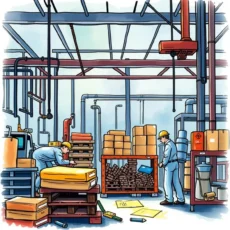
Track previous incidents for insightful patterns
The ability to document any previous incidents related to a defect promotes understanding of recurring issues within operations. By identifying historical data trends, users gain insight into systemic problems and develop proactive solutions that enhance overall quality management efforts.
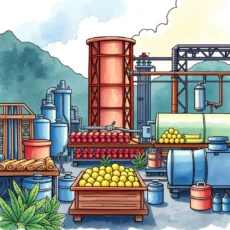
Document corrective actions taken for future reference
Recording corrective actions taken in response to defects creates a valuable history of interventions. This feature fosters accountability within teams, allowing root cause analysts to evaluate the effectiveness of resolutions over time while refining future approaches based on documented success or failure.
Additional information
Best for: Production Analyst, Operations Performance Specialist, Supply Chain Quality Analyst, Root Cause Analyst, Production Improvement Coordinator