Critical repair assistant: Determine urgent equipment issues for attention
The critical repair assistant helps schedule, prioritize and track equipment repairs, ensuring smooth operations in manufacturing and production.
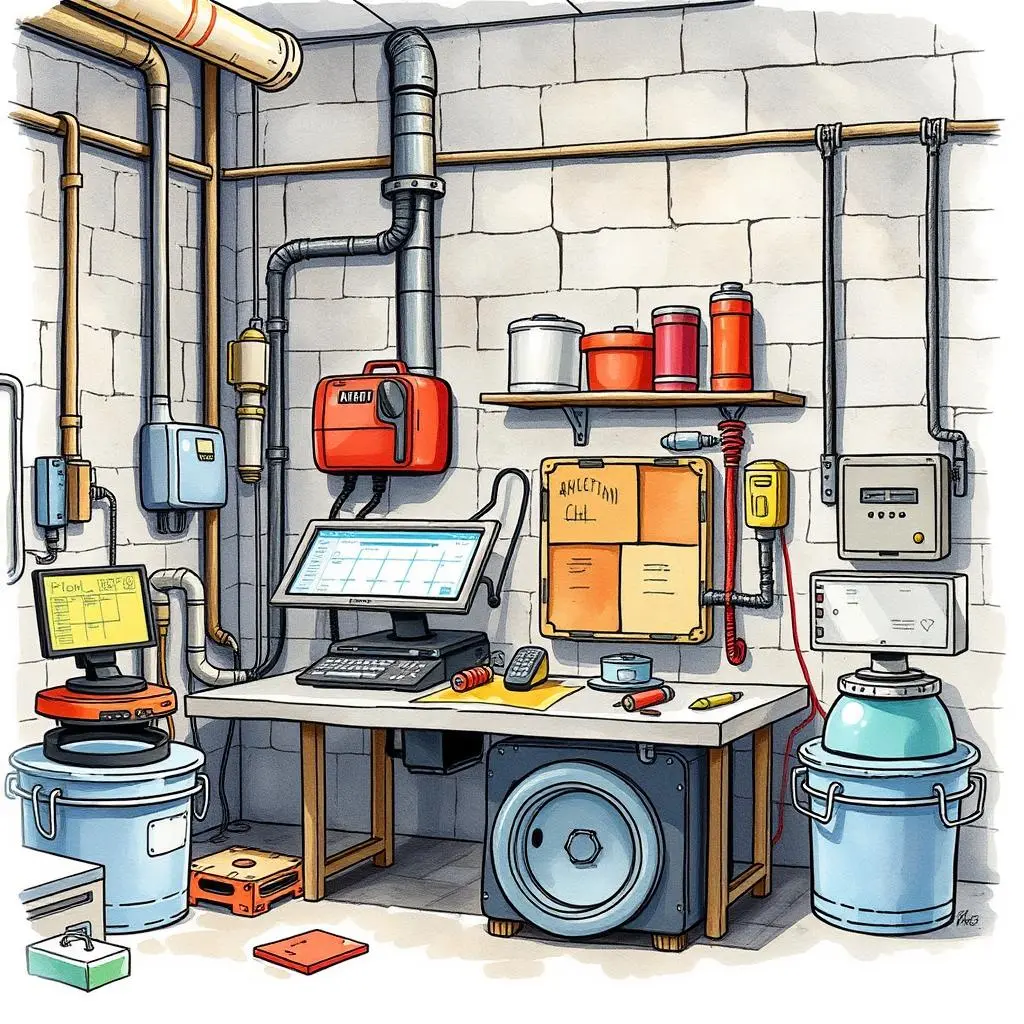
Similar apps
Additional information
Best for: Maintenance Scheduler, Equipment Maintenance Coordinator, Production Maintenance Planner, Maintenance Prioritization Analyst