Root cause analysis generator: Identify causes and solutions for production issues
The root cause analysis generator helps you identify problems, analyze impacts, and propose solutions efficiently with team collaboration.
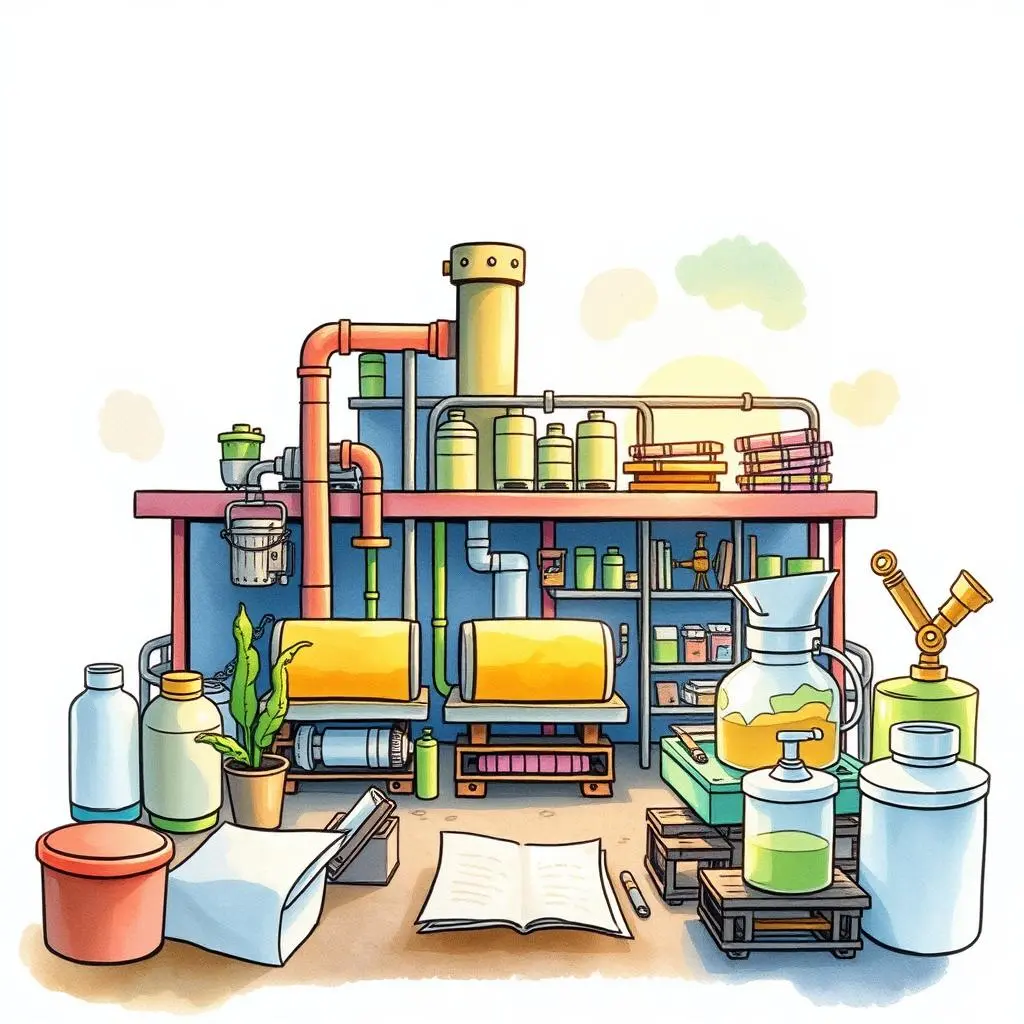
Similar apps
Powerful web app for root cause analysis and process optimization
Unlock insights and drive improvements in manufacturing
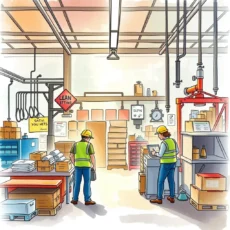
Comprehensive problem description input
Easily enter a detailed problem description to provide context for the analysis. This feature ensures all relevant aspects of the issue are captured, allowing for more accurate root cause identification and ultimately leading to effective solutions tailored to production challenges.
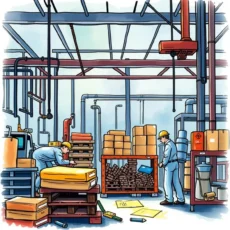
Thorough root cause identification
Input specific root causes directly into the app to streamline the analysis process. By clearly defining these underlying factors, you'll benefit from targeted solutions that can significantly enhance operational efficiency while reducing reoccurring issues in your production line.
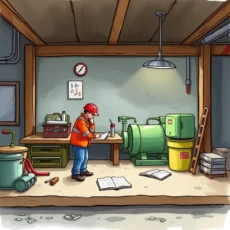
Impact assessment entry
Utilize dedicated fields to assess and note the impact of issues on production. A thorough understanding of these effects enables you to prioritize resolutions, ensuring that vital resources are allocated where they can make the most significant difference in your manufacturing processes.
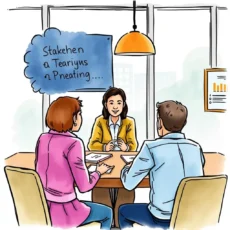
Proposed solution submission
Input suggested solutions seamlessly for each identified problem. This feature facilitates communication and decision-making among team members, allowing for quick response strategies that can be implemented during production lapses, ultimately optimizing performance across operations.
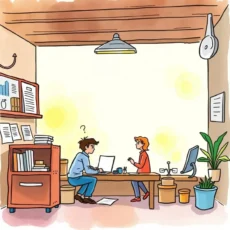
Collaborative team member input
Easily enter information about team members involved in the analysis process. Documenting participation fosters accountability and enhances collaboration among multidisciplinary teams, driving collective efforts towards effective problem-solving in manufacturing situations.

Timely analysis date recording
Specify the date of each analysis to maintain comprehensive records over time. This ensures traceability of issues and solutions implemented, empowering continuous improvement initiatives by providing valuable insights into trends or patterns within your production processes.
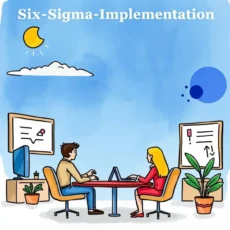
Expected outcome documentation
Clearly detail expected outcomes related to proposed solutions within the app. This function allows teams to set realistic benchmarks for improvement, encouraging goal-oriented approaches that measure success effectively while aligning with continuous improvement methodologies.
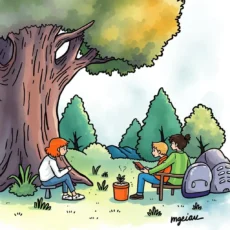
Flexible notes & comments section
Gather additional observations or feedback through a dedicated notes section. This allows users to capture spontaneous insights or contextual information not covered elsewhere, adding depth to analyses and enhancing overall understanding of production improvements needed.
Additional information
Best for: Lean Process Engineer, Continuous Improvement Specialist, Lean Manufacturing Coordinator, Process Improvement Analyst, Kaizen Facilitator