Lean performance evaluator: Evaluate success of lean manufacturing practices
The lean performance evaluator helps you analyze root causes, set success metrics, and improve processes for better manufacturing outcomes.

Similar apps
Comprehensive features of our lean performance evaluation tool
Elevate your root cause analysis with key insights
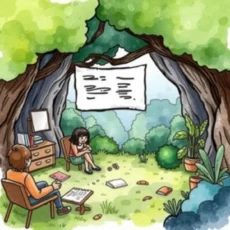
Intuitive problem description input
Easily articulate the specific issue impacting your manufacturing process by entering a detailed problem description. This foundational step ensures that the analysis is focused and relevant, allowing the tool to generate insightful feedback tailored to your unique situation.
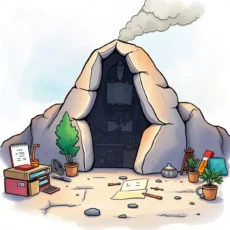
Performance metric specification
Define the exact metric you wish to establish for success in your lean manufacturing practices. By specifying this metric, you enable precise evaluations that help track improvements and substantiate ongoing enhancements in performance efficiency.
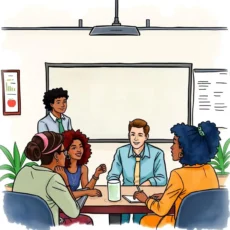
Current performance assessment
Provide insight into the existing performance level of your processes. Accurately entering this data allows for a reliable baseline comparison, enabling subsequent analysis to identify gaps and areas needing improvement effectively.
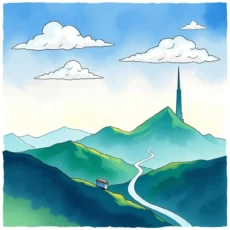
Goal setting for desired outcomes
Set clear objectives by inputting the desired performance level for your chosen metric. This feature aligns team efforts towards a common goal, making it simpler to monitor progress and stay focused on achieving results.
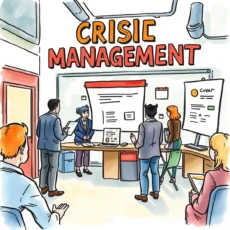
Timely achievement planning
Indicate the timeframe for reaching your desired performance levels. By establishing time-sensitive goals, you can foster accountability within your teams and enhance commitment towards achieving success through structured planning.
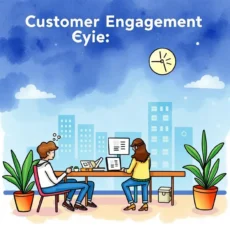
Data source integration
Input relevant data sources or supporting reports directly into the tool. This feature enriches the analysis by providing context and evidence, ensuring that decisions are backed by credible information from diverse sources relevant to root cause assessments.
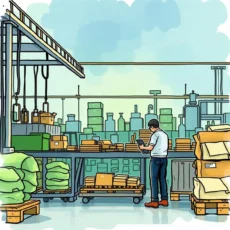
Team member engagement tracking
Detail team members involved in the root cause analysis process. This functionality enhances collaboration by promoting transparency and responsibility among all parties, ultimately leading to more effective teamwork during solution implementation.
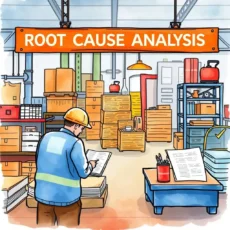
Barrier identification
Enter potential obstacles that could impede achieving desired metrics. Identifying barriers upfront allows you to proactively strategize solutions, ensuring a more streamlined path towards successful outcomes in lean manufacturing efforts.
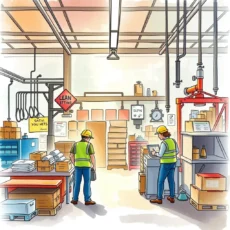
Action steps documentation
Outline actionable steps planned to address root causes effectively. Capturing these action plans ensures clarity around responsibilities and timelines while also serving as a blueprint for continuous improvement initiatives within your organization.
Additional information
Best for: Lean Manufacturing Analyst, Metrics and Performance Analyst, Continuous Improvement Specialist, Root Cause Analysis Coordinator, Operational Excellence Manager