Quality feedback excerptor: Generate concise feedback from quality inspections
Use quality feedback excerptor to streamline inspections, analyze defects, and improve product quality across manufacturing processes.
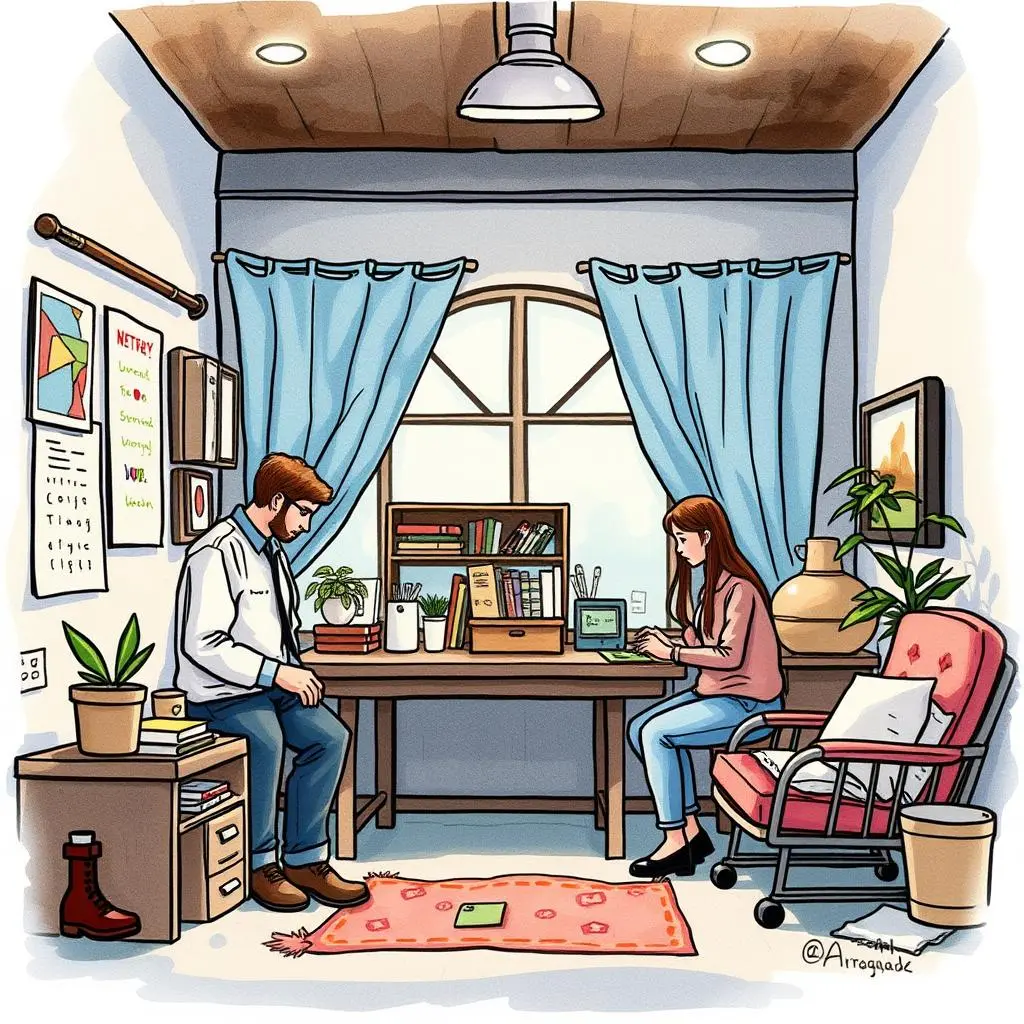
Similar apps
Boosting efficiency in quality inspections with key features
Transform your manufacturing quality processes with streamlined feedback generation that enhances productivity and accuracy
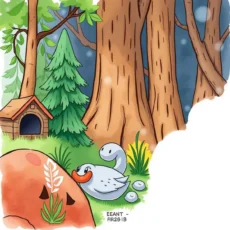
Generate concise feedback instantly
Leverage our web app’s ability to quickly process text input from inspection reports, generating actionable and concise feedback. This functionality enables Quality Control Inspectors and Managers to swiftly assess defects, significantly reducing the time spent on manual documentation.

Comprehensive data input fields
Utilize carefully designed input fields such as product ID, inspection date, and defect type. These fields ensure that all critical information regarding inspections is captured accurately, leading to improved AI output quality beneficial for Quality Assurance Specialists and Defect Analysts.
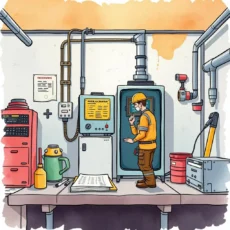
Scalable defect classification options
Easily classify defects by entering specific types like scratches or dents along with their severity levels. This feature allows for a detailed and organized approach to documenting quality issues, making it easier for Manufacturing Quality Technicians to prioritize corrective actions effectively.
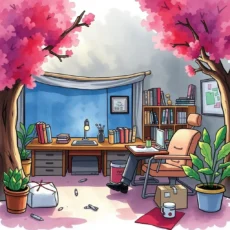
Action-oriented follow-up management
Implement a structured method for tracking necessary follow-up dates related to identified defects. By entering corrective actions taken and additional comments, Quality Control Managers can ensure ongoing improvement in manufacturing processes while maintaining comprehensive records of each inspection.
Additional information
Best for: Quality Control Inspector, Defect Analyst, Quality Assurance Specialist, Quality Improvement Engineer, Manufacturing Quality Technician