Downtime report analyzer: Summarize downtime text to optimize processes
Use the downtime report analyzer to log, analyze, and improve production downtime with clear insights and actionable corrective measures.
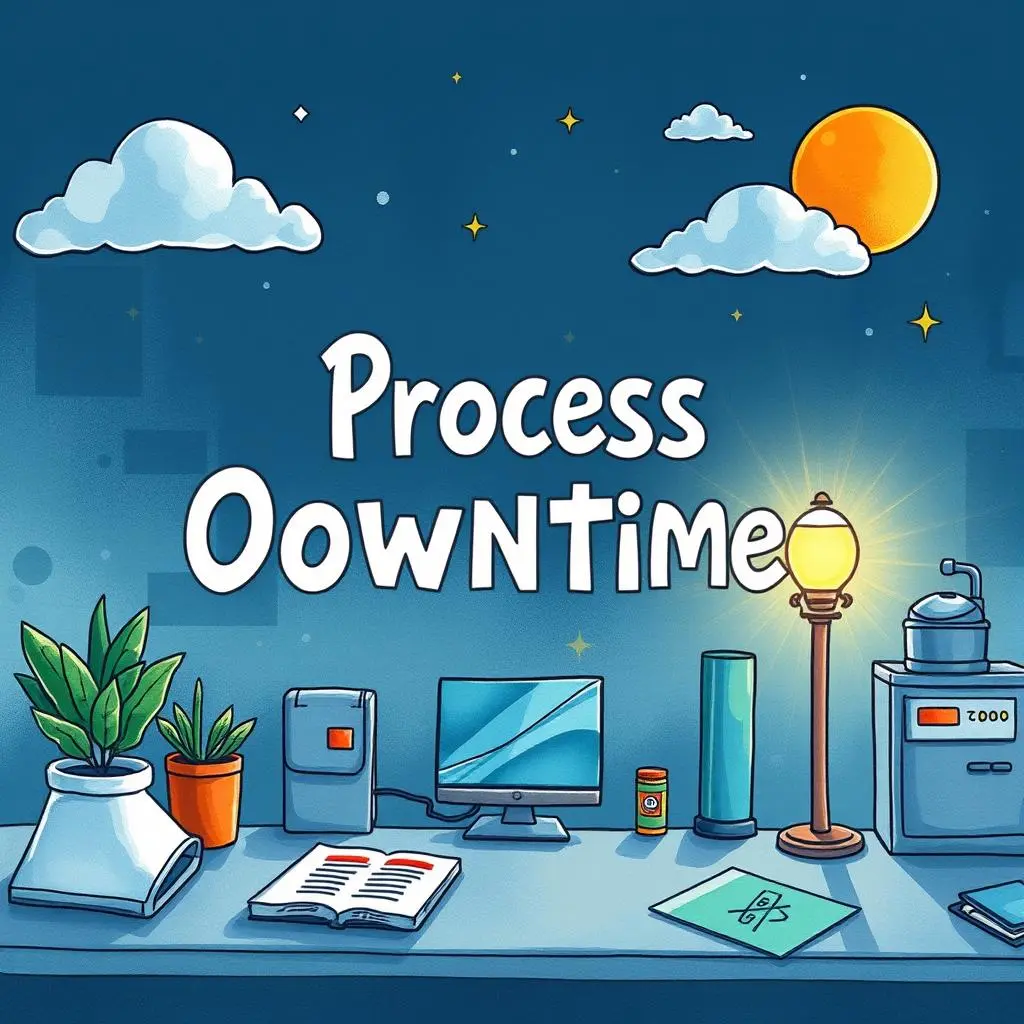
Similar apps
Maximize your process efficiency with advanced downtime analysis
Transform downtime data into actionable insights for optimized manufacturing processes and enhanced operational performance
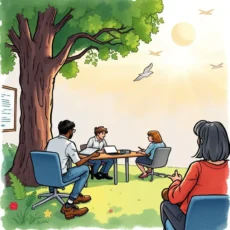
Input comprehensive downtime incident descriptions
Capture all essential elements of your downtime incidents by entering detailed descriptions. This feature ensures accurate context, allowing the app to generate meaningful summaries that inform actionable strategies for minimizing disruptions and enhancing production efficiency.
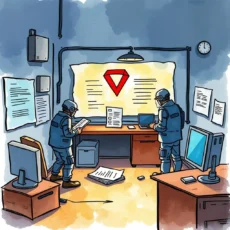
Track incident timing with precision
Easily log the date and duration of each downtime event, including start and end times. By documenting this information accurately, you enable the app to pinpoint patterns over time, facilitating strategic decisions that enhance overall process optimization.
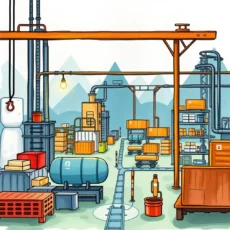
Identify affected production lines
Specify which production line or equipment was impacted during the downtime incident. This targeted data input allows for an in-depth analysis of specific operations, leading to tailored solutions that effectively address identified weaknesses in your manufacturing processes.
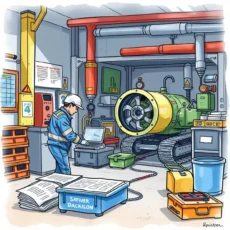
Document reasons for downtime
Record the reasons behind each incident using predefined categories such as maintenance or equipment failure. By providing this crucial insight, you empower the app to better summarize issues and suggest preventative measures that can improve operational stability.
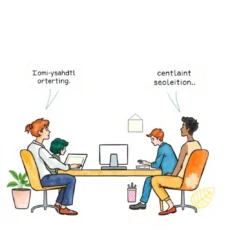
Involve key personnel in incident analysis
Include information about personnel involved in each downtime incident. This not only creates transparency but also fosters a collaborative approach towards continuous improvement by ensuring that those accountable are engaged in finding solutions to recurring issues.
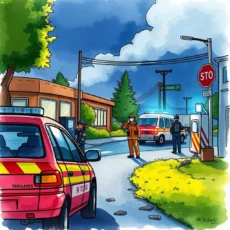
Outline corrective actions taken
Detail any remedial measures implemented post-incident directly within the input form. This adds valuable context to each case, enabling a more comprehensive understanding of effective strategies on how minor adjustments can lead to significant improvements in future operational practices.
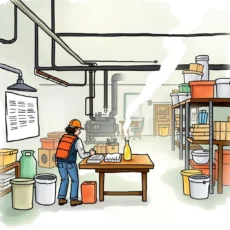
Add comments for additional insights
Provide any extra observations or comments related to downtime incidents through designated input fields. Integrating these insights allows for richer analysis from the AI model, resulting in well-rounded summaries that encompass all facets of your process efficiency efforts.
Additional information
Best for: Process Improvement Specialist, Continuous Monitoring Analyst, Manufacturing Process Engineer, Operational Excellence Coordinator, Lean Manufacturing Consultant