Standards comparison tool: Generate comparative analysis of process standards from text
Use the standards comparison tool to streamline auditing tasks, identify gaps, and propose improvements for better engineering quality.
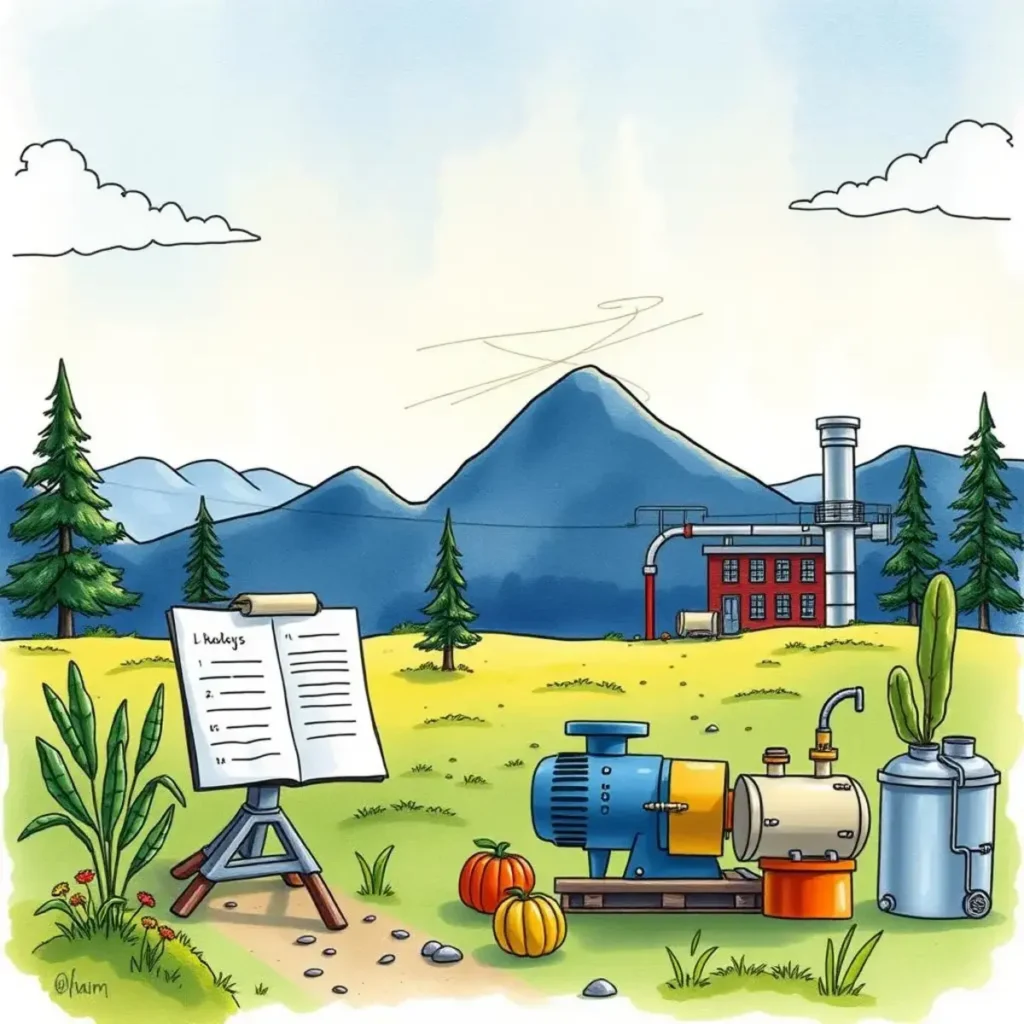
Similar apps
Unleash the power of comparative analysis for process standards
Streamline your process improvement efforts with advanced tools
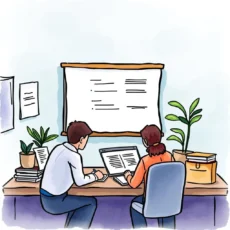
Comprehensive text input for detailed audits
Effortlessly enter detailed process descriptions, audit dates, team members involved, and identified issues or gaps. The flexibility to input key information ensures that your analysis is thorough, allowing the tool to generate targeted insights that drive effective process improvements.
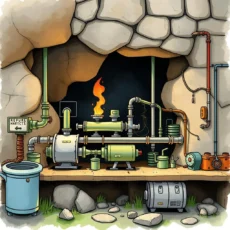
Focused outputs to identify improvements and outcomes
Your inputs concerning proposed changes and expected outcomes are processed to deliver insightful comparisons. This feature helps Quality Engineers and Process Improvement Specialists to pinpoint areas needing attention, enabling well-informed decision-making that fosters continuous improvement.
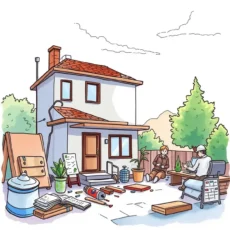
Custom follow-up actions and recommendations generation
Capture necessary follow-up actions required from your audits. This feature not only documents the next steps effectively but also aids Compliance Auditors in tracking progress, ensuring accountability within teams while aligning with compliance standards.
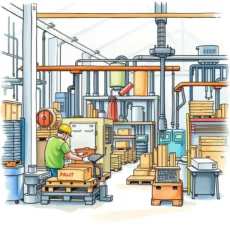
Scheduled audit tracking for sustainable improvements
By entering the next audit date, users can systematically schedule follow-ups and maintain consistency in evaluation processes. This organized approach encourages ongoing optimization of processes, catering specifically to Continuous Improvement Managers’ objectives for operational excellence.
Additional information
Best for: Quality Assurance Auditor, Process Improvement Specialist, Quality Engineering Analyst, Continuous Improvement Manager, Process Audit Coordinator